Module bestehen meist aus Stahl oder Holz, da beide Materialien leicht und tragfähig sind. Ein Besuch in zwei Werkstätten: bei Cocoon in Pratteln und bei Renggli AG in Schötz.
Vom Profil zum Modul
Tausendfach stapelt sich das Produkt ab Stange und besetzt die halbe Halle in einem Gewerbegebiet in Pratteln, wo Bombardier früher Eisenbahnwagen herstellte: C- und U-Profile aus Metall, viele Meter lang, nur rund zwei Millimeter dick. Ein grosses Lager heisst grosse Flexibilität, kurze Lieferzeiten. «Transformer» nennt der Stahlleichtbauer Cocoon die Elemente, aus denen Balken, Träger, Stützen, Wände und später Module werden.
Cocoon ging aus einem Gipsergeschäft hervor, das sich auf Stahlleichtbau spezialisierte. Ihre Profile kamen beim Schaulager in Münchenstein, beim Zentrum Paul Klee oder beim Shoppingzentrum Westside zum Einsatz. Stahl ist extrem belastbar, die Dimensionen sind somit schlank. Das Material ist ideal, um den Bestand aufzustocken und Verdichtung voranzutreiben. Als Spezialist für Elementbau beteiligte sich Cocoon am Forschungsprojekt «Living Shell» der HSLU in Zusammenarbeit mit LAST EPFL, das diese Anwendung erforscht hat siehe Seite 15, Forschen mit dem Modul. Für Stahl spricht laut Marketingleiter Daniel Seiler auch die graue Energie: «Bis zur Hälfte unseres Stahls stammt aus Rezyklat», sagt er, fügt aber an: «Für das Modul spielt es keine Rolle, ob es aus Stahl oder Holz gebaut ist.»
Zusammenschrauben unnötig
Langsam beisst sich das Sägeblatt in den Stahl, der Lärm betäubt die Ohren: Ein Spengler schneidet verschiedene Profile auf die richtige Länge zu. Insgesamt 190 Stück in verschiedenen Dimensionen arbeitet er von der Liste ab. Ein anderer «verclincht» zwei Profile zu einem Doppel-T-Träger. Mit Luftdruck presst er dazu einen Bolzen in das Metall, um die zwei Profile ohne weitere Hilfsmittel zu verbinden. So entfällt auf der Baustelle die Schraubarbeit. Ein Etikett auf jedem Profil zeigt den Monteuren später an, wohin es gehört: «Geschoss 5, Wand 1.» Nach der Konfektionierung gelangen die Profile entweder direkt auf die Baustelle – oder aber zuerst zu einem Holzbauer, der sie zu Wandelementen oder ganzen Raumzellen montieren wird.
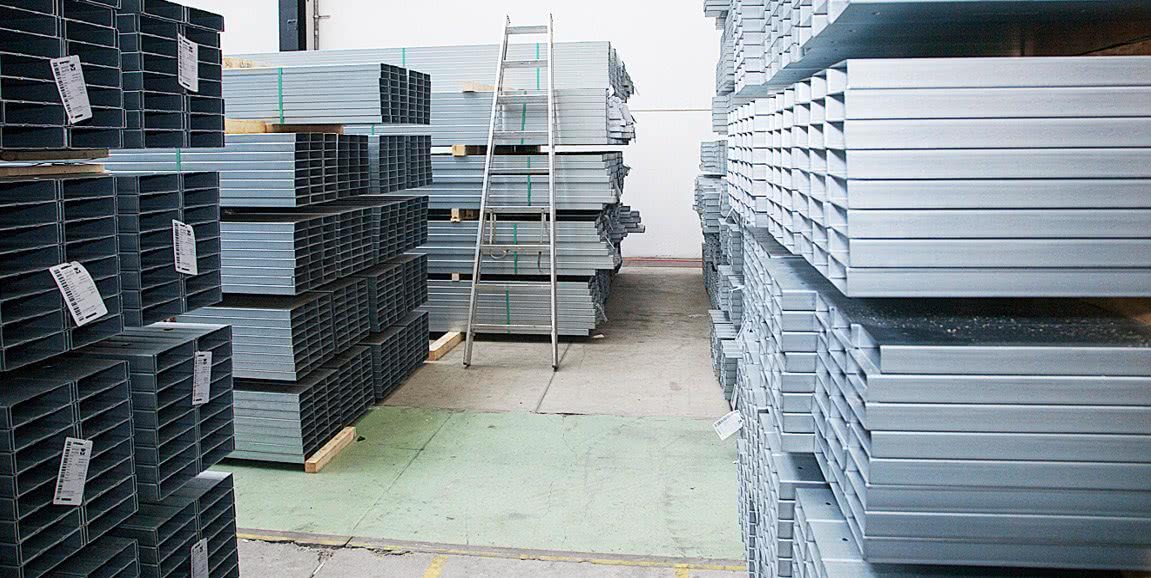
Für das Modul spielt es keine Rolle, ob es aus Stahl oder Holz gebaut ist.
Daniel Seiler, Marketingleiter Cocoon
Zuschnitt auf Knopfdruck
Schötz liegt im Luzerner Hügelland. Bauernhöfe, Felder, Wiesen. Neben einem alten Holzhaus der Zimmerei Renggli grasen Ponys. Dahinter endet die Idylle. Was 1923 mit einer Sägerei begann, ist heute auf 200 Angestellte angewachsen.
Das Lagersystem holt auf Knopfdruck die passende Platte aus dem Gestell und legt sie für die Zuschnittmaschine bereit, die das massgeschnittene Brett keine Minute später nummeriert ausspuckt. «Wir bereiten die Daten der Architekten auf und schicken sie an die Maschine», erklärt Filli. Mit der digitalen Gebäudedatenmodellierung (BIM) werde das künftig noch einfacher gehen, prognostiziert er. Auch der Abbund funktioniert automatisch. Die Kappanlage sieht Fehler im Holz und lässt sie aus. Eine andere Maschine sägt 12 Meter lange Balken zu, fast sie ab, bohrt sie an. «Die computergesteuerte Fertigung belebt alte Konstruktionen wieder», sagt Filli. In der Hand hält er eine Schwalbenschwanzverbindung, die man früher aufwendig mit dem Stechbeutel fertigte – für die Maschine eine Sache von Sekunden. Auf der anderen Hallenseite beginnt die Handarbeit. Ein Arbeiter legt Balken auf den Maschinentisch, Stahlnocken richten sie rechtwinklig aus. Dann beplankt er sie mit einem Brett. Der «Schmetterlingstisch» wendet bis zu 14 Meter lange Elemente: Er klappt die Flügel hoch und dreht sie auf den Rücken. Eine Station weiter füllen Zimmerleute ein Wandelement mit Dämmung, verlegen Elektrorohre, schrauben Fensterrahmen fest, kleben Luftdichtfolien. Bei Innenwänden montieren sie Gipsplatten, bei Fassaden die Verkleidung.
Millimetergenau auf zehn Meter
Es riecht nach Holz, im Hintergrund surrt ein Sägeblatt, die Nagelpistole ploppt dumpf. «Die hohe Vorfertigung ist unsere Spezialität», sagt Filli. Das hat seinen Preis. Die Infrastruktur im Werk kostet mehr als beim Bauen vor Ort. «Über den ganzen Lebenszyklus ist die Vorfertigung günstiger», ist Filli überzeugt. «Im Werk können wir unter perfekten Bedingungen eine massiv höhere Qualität umsetzen.» Zudem verkürze sich die Bauzeit vor Ort. Die Präzision zeigt sich an den Ecken, wo die schräg zugeschnittenen Latten aneinanderstossen. Ein zehn Meter langes Element muss millimetergenau passen, sonst rümpft der Bauherr die Nase. Auch die Höhen, zu denen sich Holzbauten neuerdings aufschwingen, erfordern Genauigkeit. «Mit jedem zusätzlichen Geschoss würden sich die Abweichungen weiter kumulieren», sagt Filli. Das Verhältnis von Eigengewicht zu Traglast sei bei Holz unschlagbar. «Im Verbund mit anderen Materialien liegt dennoch oft ein Vorteil», sagt er. Etwa wenn die Statik mit Stahl oder der Brandschutz mit Beton optimiert werde.
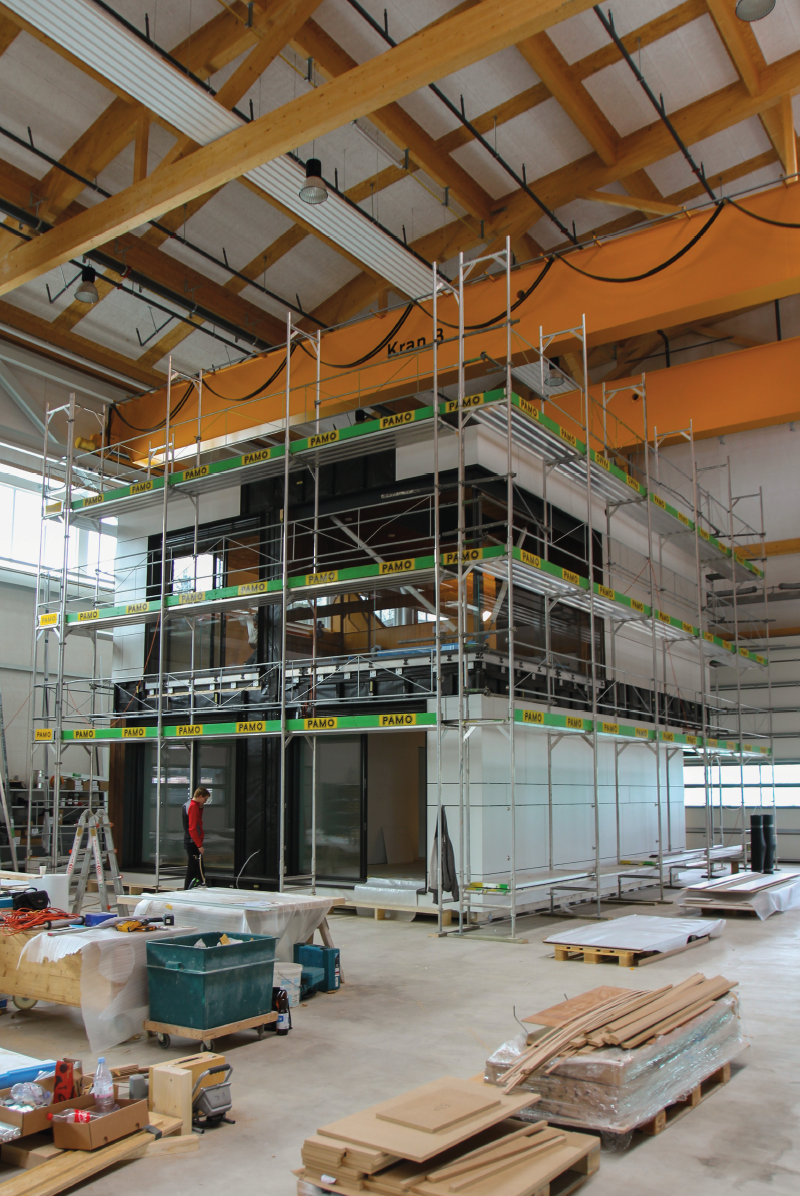
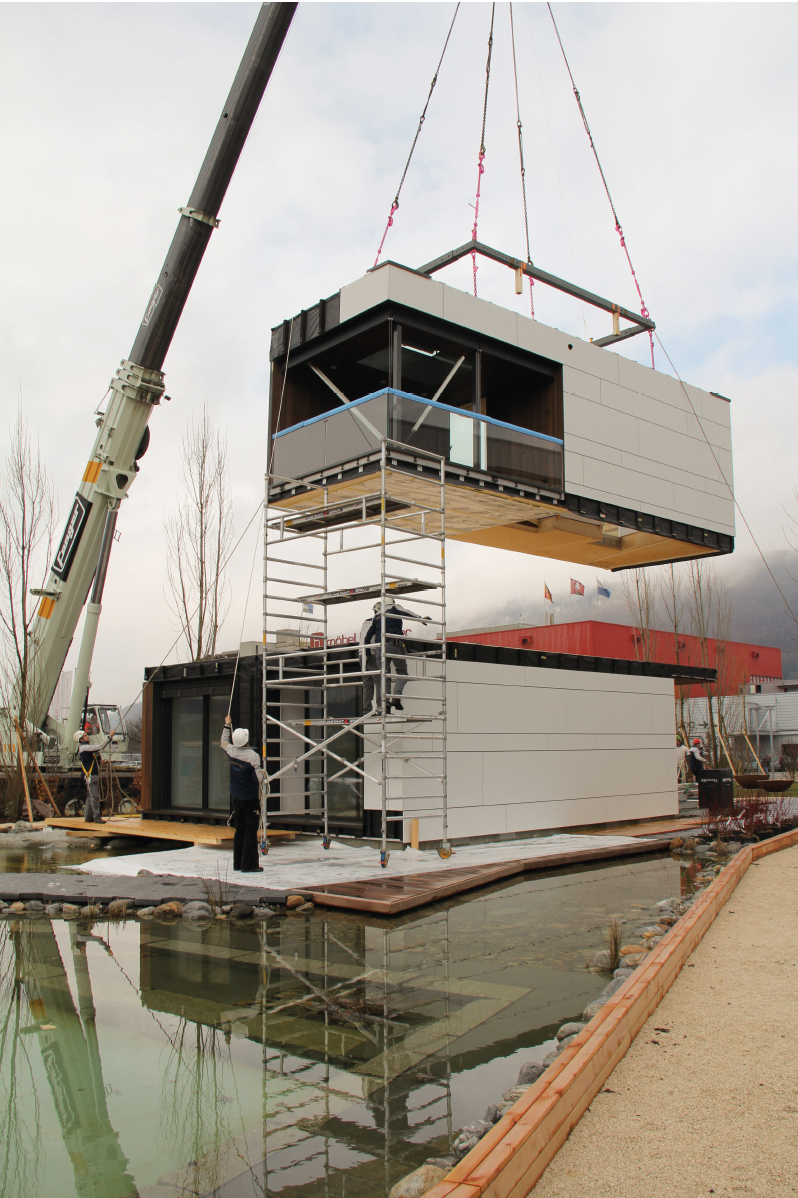
Renggli baute das Moduleinfamilienhaus testhalber in der Halle auf. Danach wurde das Gebäude in Rothrist vor Ort definitiv zusammengesetzt.
Bild: Renggli
Transport setzt Grenzen
Die fixfertige Wand kommt in ein Gestell, bis der Lastwagen sie holt. Raummodule gehen einen Schritt weiter. Aus den Wand- und Deckenelementen baut Renggli ein kleines Häuschen. Sein Mass beeinflusste die Dimension der Werkhalle, deren Holzträger sich über die Arbeiter spannen: Die 16 Meter Höhe erlauben, zwei Module übereinanderzuheben. Der Spielraum war für die Einfamilienhausreihe «Vision: R4» nötig. Das Testhaus aus vier Modulen hat Renggli samt Möblierung in der Halle aufgebaut, um alle Details zu prüfen. Später wurde es zerlegt, abtransportiert und in drei Stunden in Rothrist AG aufgestellt. Der Transport bestimmt den Holzbau – und noch mehr das Bauen mit Raummodulen. «Wir müssen die Grösse der Bauteile oft auf die Zugänglichkeit der Baustelle abstimmen», erläutert Filli. Bei den grossen Module kommt ein Lastwagen zum Einsatz, dessen Ladefläche tiefergelegt ist. Bei vier Metern Höhe ist Schluss. Für ein Gebäude im Tessin musste Renggli einst sogar den Gotthardtunnel sperren lassen, damit der Lastwagen mit seiner breit ausladenden Fracht in der Mitte der Röhre fahren konnte. Ein Modul wiegt schnell 10 bis 20 Tonnen. «Wir berechnen die Aufhängepunkte genau», sagt Filli. Sonst hängt das Modul später schief am Kranseil, dabei verzöge sich die Konstruktion mit den fertigen Oberflächen. Marco Filli tritt aus der Werkhalle auf den Hinterhof, wo mit weisser Folie eingepackte Anhänger auf die Fahrt zur Baustelle warten. Am Rand des Grundstücks steht ein Häuschen, klein wie ein Schiffscontainer.
Modulbau bedeutet aber nicht zwingend Askese. Rengglis R4-Einfamilienhaus trumpft mit Skyframe-Fenstern, Minergielüftung und Bodenheizung auf. Trotzdem: Am geeignetsten sei modulares Bauen nach wie vor für temporäre Bauten, also Provisorien für Schulen, Spitäler oder Asylheime. Das Swisswoodhouse, das Renggli mit Bauart entwickelt hat, wurde zwar in einer modularen Struktur geplant, aber mit Elementen gebaut. «Das Modul lebt von der Wiederholung», so Filli. «In der Schweiz will aber jeder ein individuelles Zuhause». Doch wer weiss, überlegt er, vielleicht ändere sich dies mit der Verdichtung schon bald.
Die hohe Vorfertigung ist unsere Spezialität.
Marco Filli, Renggli Holzbau
Modulart Partner
Erfahren Sie mehr über die Renggli AG und über die Entwicklung des Swisswoodhouse.
Schreiben Sie einen Kommentar
Ihre E-Mail-Adresse wird nicht veröffentlicht. Erforderliche Felder sind mit * markiert.